
Energy self-production pays off: The powerful Kombi Power System supports you as a reliable partner at the location of your choice. Stay independent of rising energy prices and cover your individual energy needs in a cost-saving and climate-neutral way.
The operation of the Kombi Power System
The updraft gasifier forms the heart of our plant. In a special combustion chamber, the raw gas obtained is burned cleanly and efficiently in startup and shutdown mode as well as in pure heat mode. The connection of supplementary modules is individually tailored to your energy requirements.
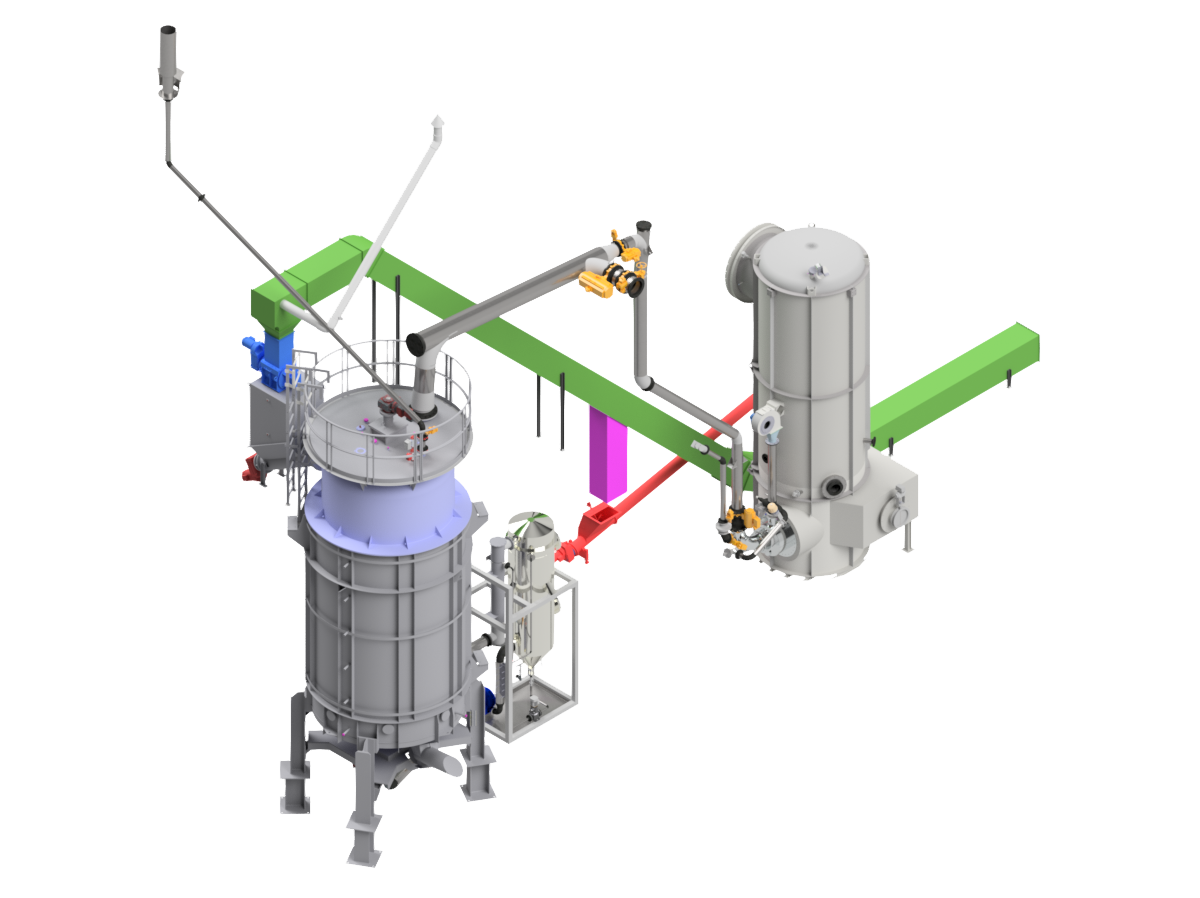
Fuel feed
Combustion chamber
updraft gasifier
Choose the energy combination that best suits your needs:
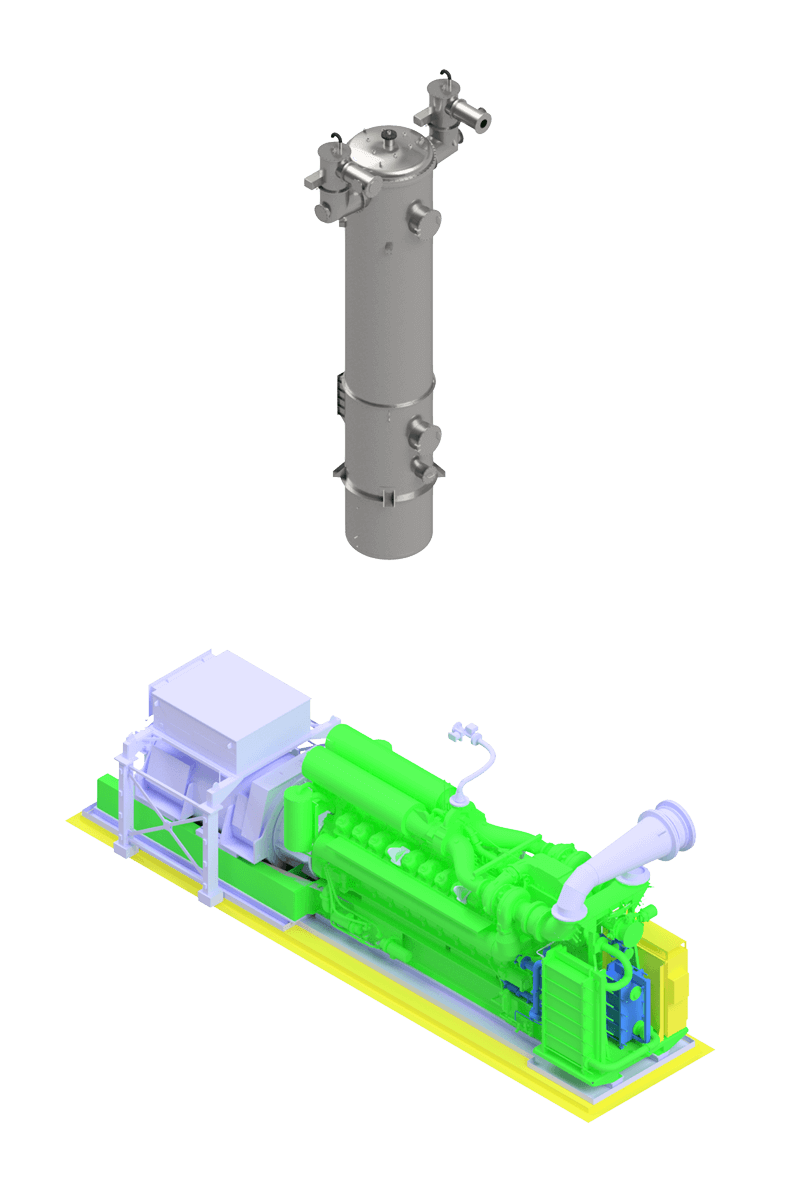
Combined heat and power plant
Kombi Power System with combined heat and power unit
If the system is to be combined with a combined heat and power unit, raw gas is cooled and filtered in 2 stages before entering the gas engine. The cooler and filter are largely maintenance-free.
The bio-oil (pyrolysis oil) exhausted in the process can then be used in the combustion chamber to generate heat on demand or can be discharged as a feedstock for fuel production.
- electricity
- bio-oil
- synthesis gas
- heat
Process gas as the energy form of the future
Fossil fuels are still popular energy sources for heat supply. In the search for environmentally friendly alternatives to natural gas, heating oil or pulverized lignite, process gas offers a high-quality solution.
The product obtained from the updraft gasifier is in no way inferior to conservative raw materials; on the contrary, you gain a significantly better environmental balance for the same output.
Other options for process gas utilization:
- Industrial furnaces
- hydrogen production
- fuel production
- biomethane
- synthesis gas
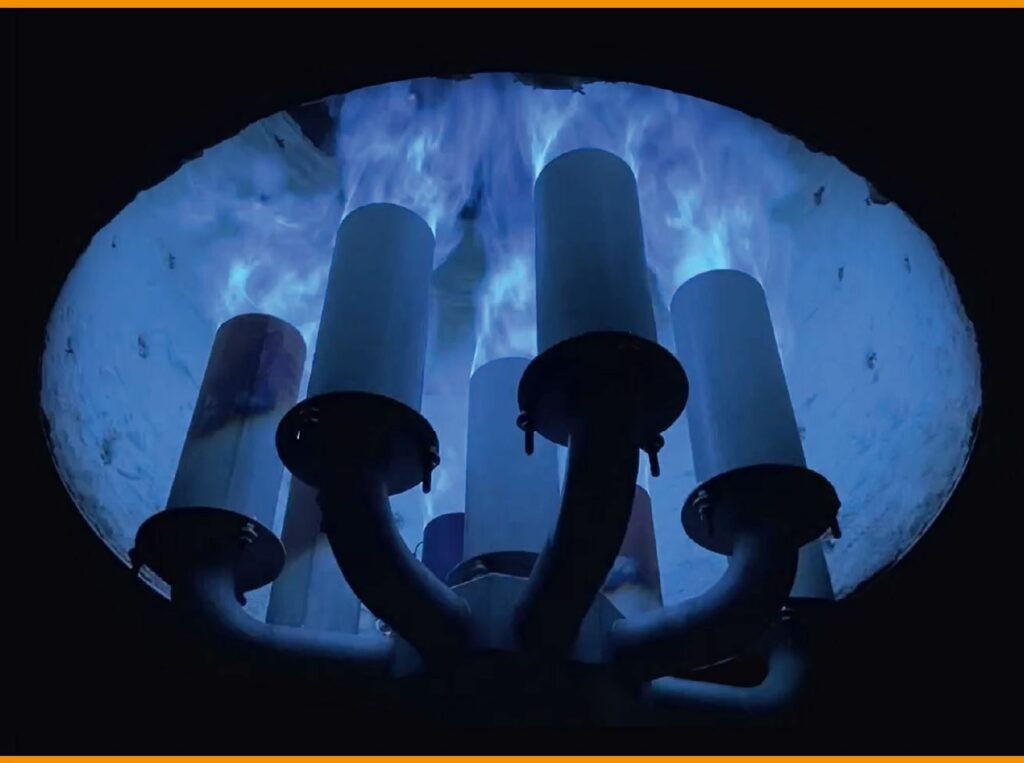
Individual heating solutions
In order to make the best use of the heat from the combustion chamber, various heating solutions are available depending on requirements.
Hot water
Hot water boiler for flow temperatures up to 135°C.
steam
Steam boiler with feedwater preheater for highest efficiencies up to 30 bar.
Thermal oil heater
Thermal oil heater with economizer for supply temperatures up to 315°C.
- heat
- steam
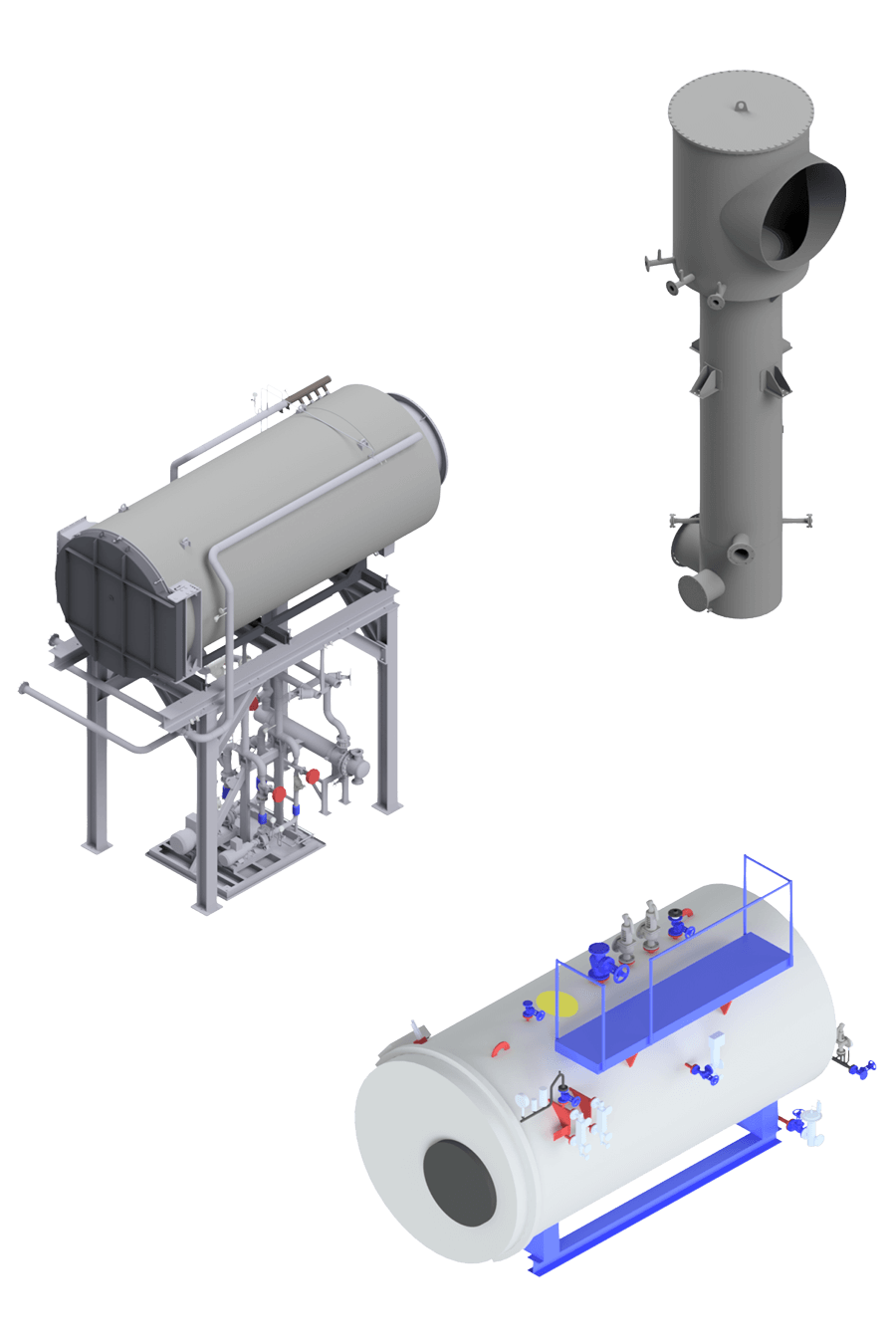
Use thermal oil efficiently
For coupled power and heat generation, a thermal oil heater can be used in combination with a thermal oil ORC system.
- electricity
- heat
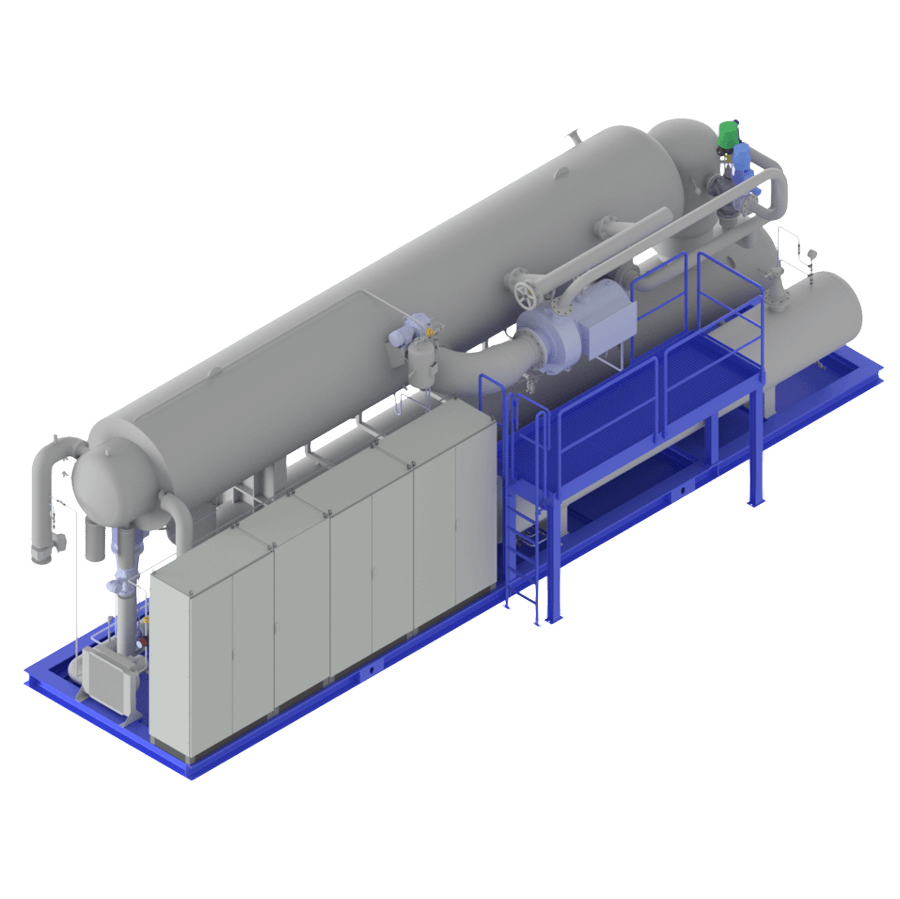
Using flue gas efficiently
In a direct evaporator ORC plant, flue gas circulation allows the clean flue gas recovered from the combustion chamber to be used for coupled power and heat generation.
- electricity
- heat
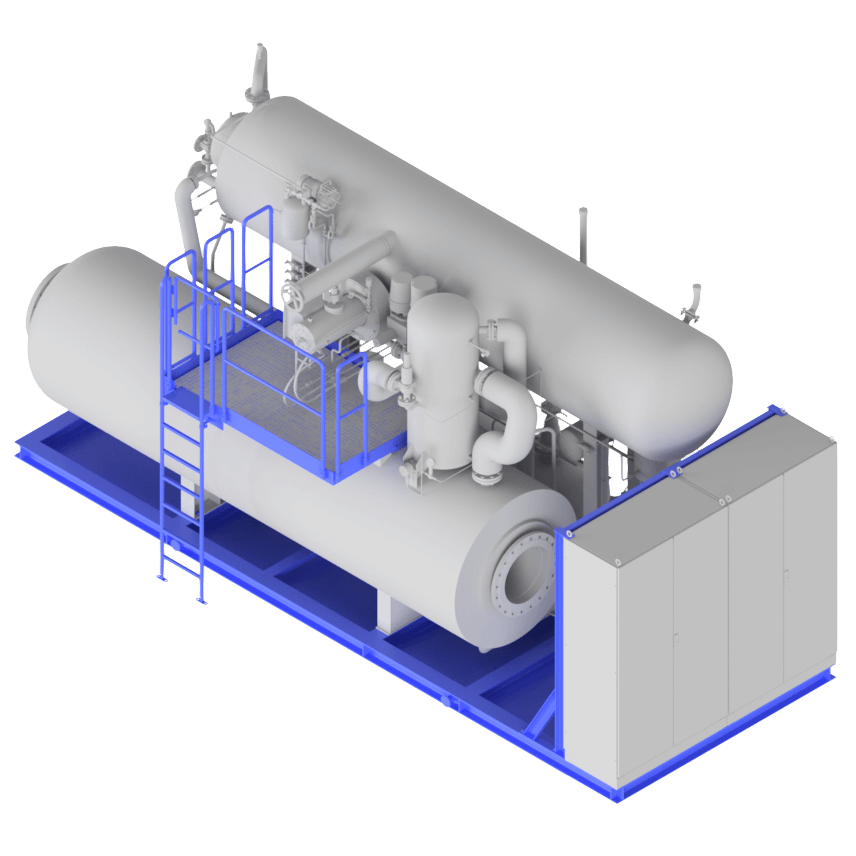
ABSORPTION COOLING MACHINE - Generate Cold Through Heat
The waste heat from the combined heat and power plant is ideal for refrigeration. An absorption ch iller generates cold water that can be used as process cooling or for air conditioning.
In the following diagram, the exact process of cold generation is clearly illustrated.
- cooling
Highest effectiveness Until the end
Various boiler types with economizers are used as standard for flue gas utilization
In addition, a flue gas condensation unit can be installed. This is used for maximum flue gas heat recovery with additional low-temperature heat utilization.
The exhaust gases are characterized by a high water vapor content. By cooling below the dew point and condensing this exhaust gas moisture, up to 40% of the fuel heat can be recovered.
The following applies here:
The lower the network return temperature (or at least a partial flow from it), the higher the heat recovery.
- heat
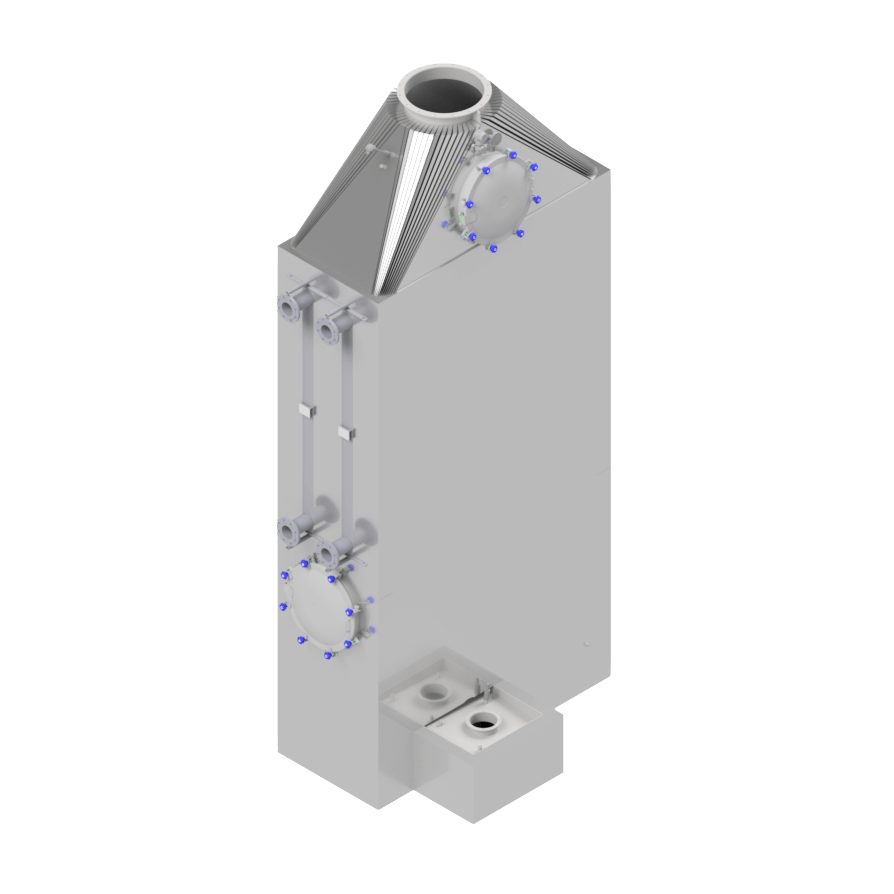
Possible locations:
- Energy-intensive commercial enterprises such as:
- Joineries
- Dairies
- Breweries
- Greenhouses
- Sawmills and wood mills
- Other uses:
- Industry with process heat demand
- Local and district heating networks
- Municipalities and cities
Technical data:
-
Power electric 250-2000 kW
-
Gasifier size 2.0-2x4.5 MW
-
Fuel heat output 1200-7000 kW
-
Fuel requirement 1,7-10 Sm³/h
-
Optional: Flue gas condensation 226-1332 kW
-
Total heat output HT 523-2744 kW
-
Total heat output HT+NT 850-5200 kW
-
Space requirement Kombi Power System300-600 m² H=15m
Why choose the Kombi Power System?
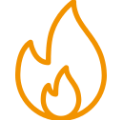
Fuel
- No pre-drying of the fuel necessary
- Robust conveyor technology allows large and lumpy fuels
- Fuel diversity: waste wood, forest chips, landscape wood, screenings from composting plants, bark, etc.
- Continuous range expansion through tests at our pilot plant
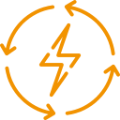
Efficiency
- The modular design enables maximum flexibility with the greatest possible efficiency.
- Fuel burnout is complete, leaving behind pure ash.
- High cold gas utilization rate: The gas outlet temperature is only 75° C
- The Kombi Power System impresses with the best possible heat utilization concept
- High efficiency due to the updraft principle
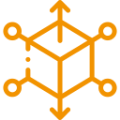
Scalability
- The Kombi power system is capable of partial load and is controllable during operation.
- The plant can also be expanded and adapted at a later date.
- Due to the updraft principle, upscaling and downscaling are very well possible.
The look into the future
The energy issue of the coming years is more complex than ever. This makes it all the more important to understand the trends shaping our industry and to provide innovative answers.
With the continuous optimization of our system, we can offer a sustainable energy solution with forward-looking prospects.
Alternative fuels
A wide variety of production residues, such as nutshells, are suitable as an excellent fuel. In our pilot gasifier, we are already testing this alternative for use in everyday operations.
Other alternative fuels
- Miscanthus
- Sewage sludge briquettes
- Agricultural residues
- Plastics
- Residual materials from the food industry
- Inferior wood briquettes
reFuels / Biomass to liquid (btl)
To get closer to the step of climate-neutral energy generation, we supply the basic material for reFuels and other sustainable fuels. For example, we are investigating the use of bio-oil as a basis for fuel production in a funding project with the FNR.
For example, simple processing steps for the production of fuels for robust marine diesel engines, more complex refinery processes for the production of high-quality fuels, and Fischer-Tropsch syntheses are available.
Hydrogen
A special process enables us to produce particularly reactive raw gas, which is then further processed. The reactive gas, which consists mainly of water, carbon dioxide and monoxide, methane and hydrogen, enables a hydrogen yield of up to 40%. Through further reforming and final PSA, the hydrogen content can be increased to over 99%.
Bio-methane
In a pilot project, we are researching the possibility of obtaining bio-methane from biomass heating (power) plants that can be used for synthesis processes. In collaboration with the Friedrich-Alexander University (Erlangen-Nuremberg) and our cooperation partner prosio engineering, we have set ourselves the task of developing an effective alternative to fossil fuels: "green natural gas".
We expect this project to result in an innovative technology with great impact and rapid market availability.
Our reference plants
From the first contact to the finished plant
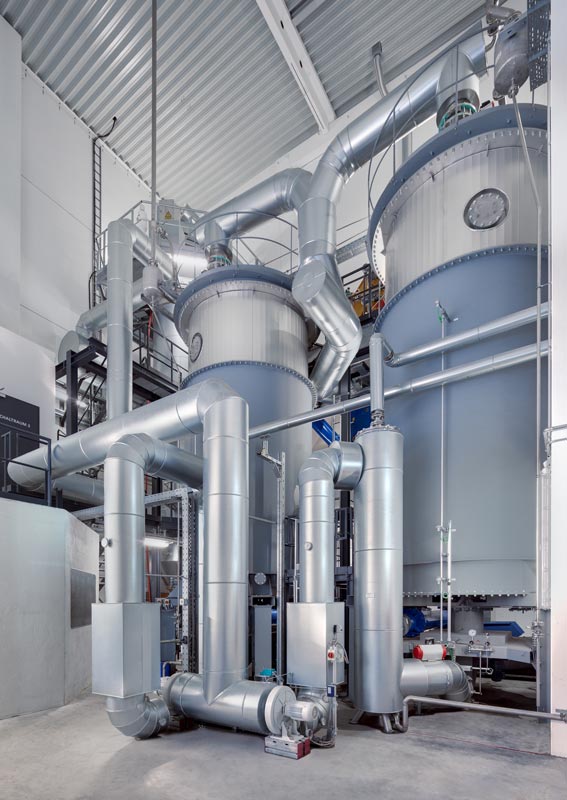
- After your initial inquiry, let us know your energy needs. We will be happy to assist you in determining them.
- Based on the determined data and the site-specific conditions, we start planning your individual Kombi Power System.
- Together with our partners, the construction of your plant will be implemented.
- After about one year of construction, we hand over the turnkey plant to you and put it into operation.